ていねいな仕事から生まれる「森の家具」
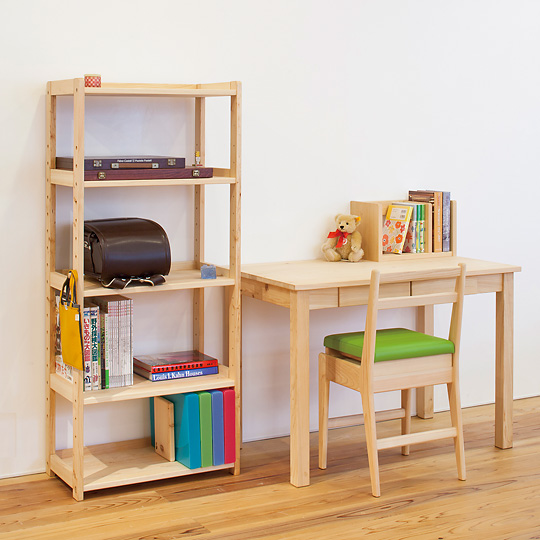
静岡県産のヒノキを使って、静岡市で製作されている「森の家具」シリーズ。百町森のスタッフで工場見学に行ってきました。
自然豊かな環境
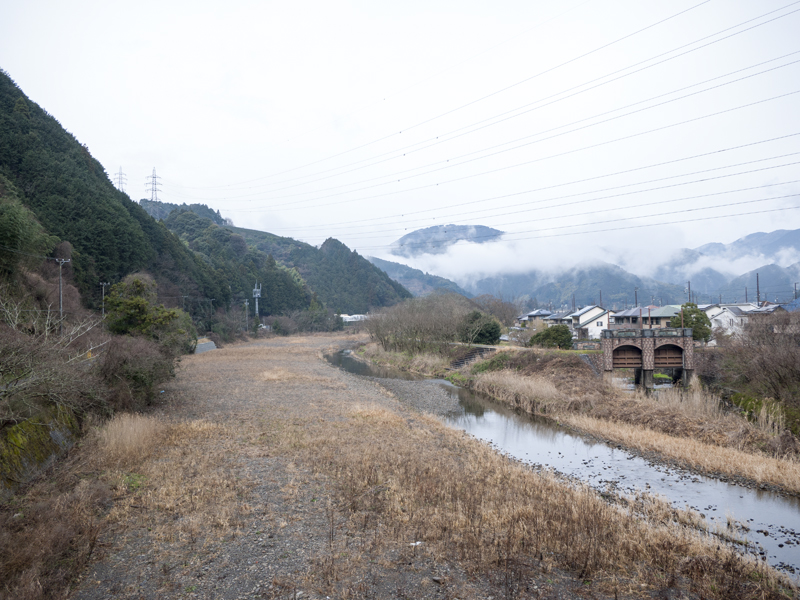
静岡市内を流れる安倍川を上ったところに工場はあります。雨上がりでもやがかかっていました。
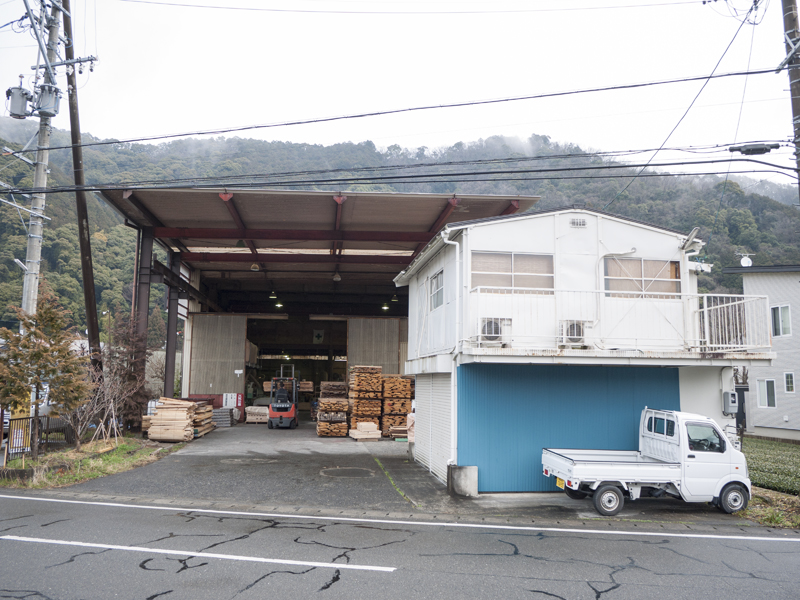
工場は茶畑に囲まれていて、背後に山も見えています。
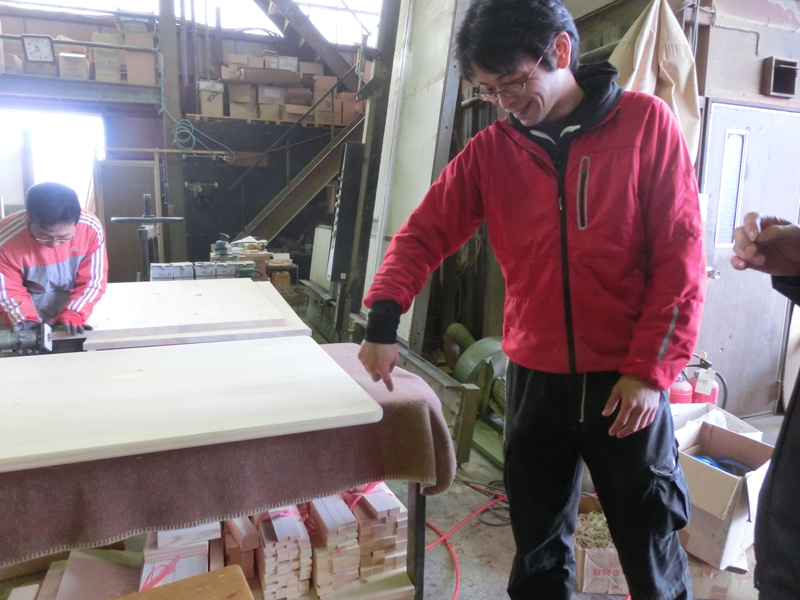
笑顔が印象的な工場長の山梨さんに案内していただきました。若くてビックリ。
材料
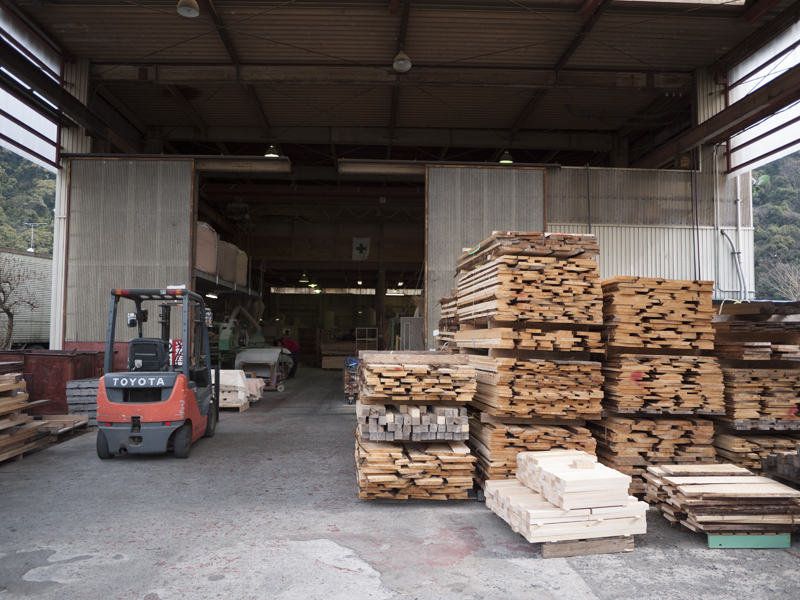
工場の入り口前の屋根ありスペースに材木置き場があります。
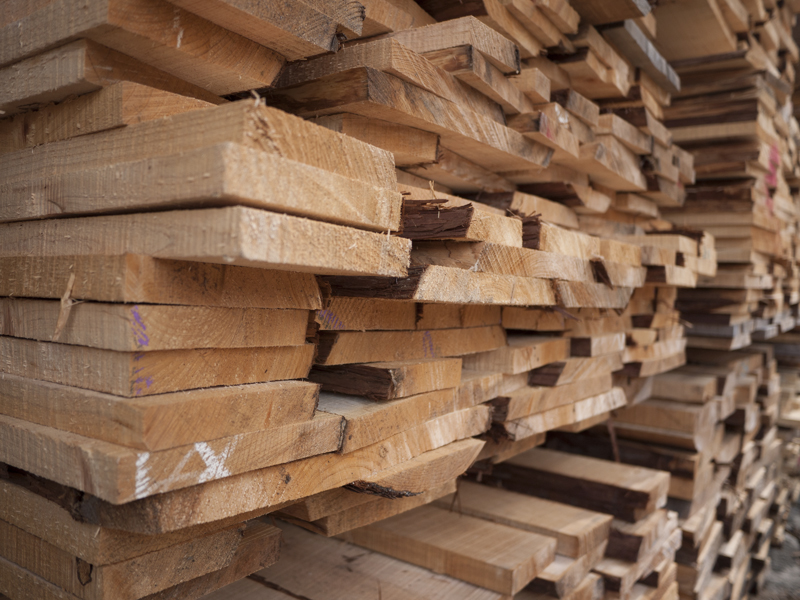
製材して人工乾燥されたヒノキ材を使用します。15mmから60mmくらいまで、色々な厚みの材料を使うそうです。
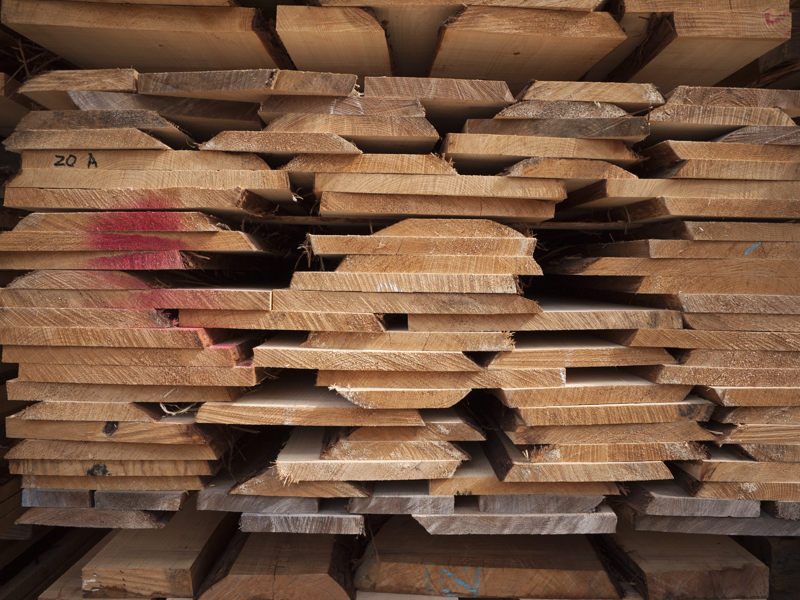
商品の仕上がり厚よりも5~10mmほど厚みのある材料を使います。ほとんどがヒノキですが、机の引出しの底板用の杉板もあります。材木に詳しいベテランの社員さんが買い付けてくるそうです。
工場内
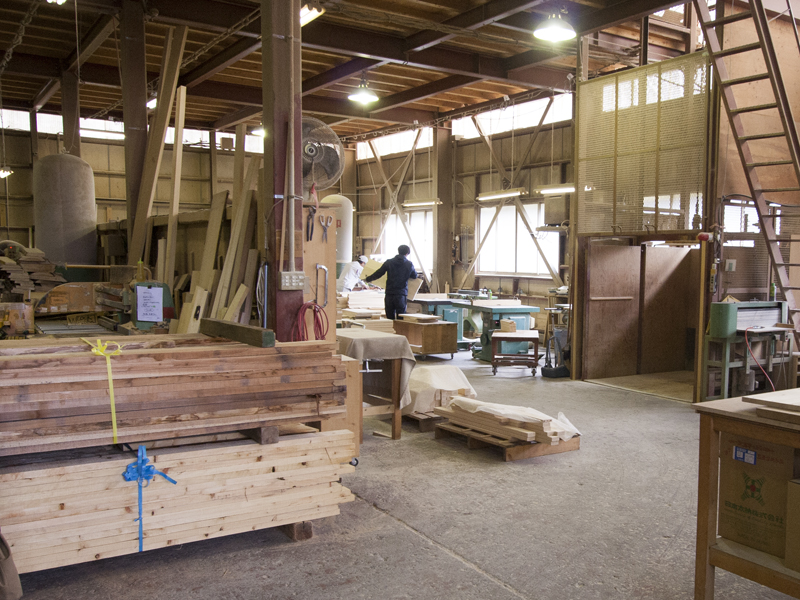
さて、工場に入りましょう。中は綺麗に整理整頓されています。工程は大きく「木取り」(写真左側)と「加工」(写真右側)に分かれています。
木取り工程
ここでは、だいたいの長さを決め、幅を落とします。
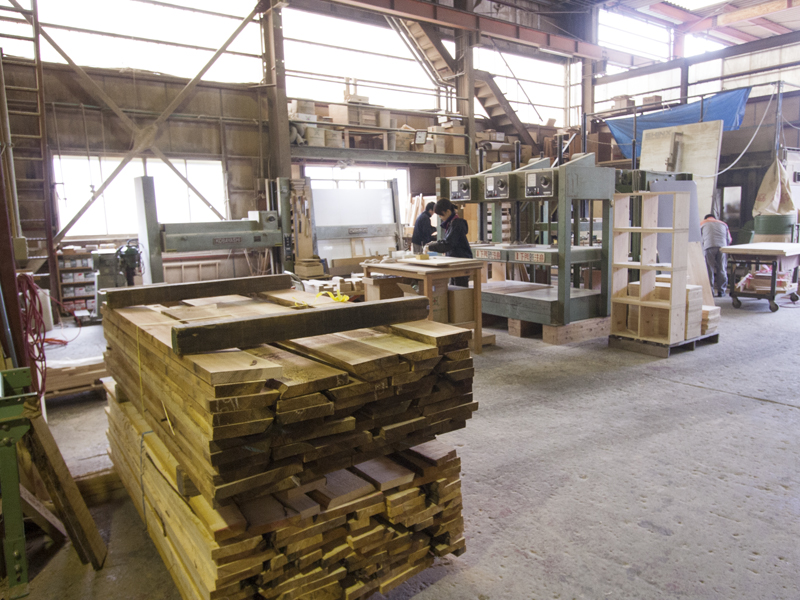
外に置いてあった材料は、フォークリフトでここに運び込まれます。
長さ切り

運び込まれた2mほどの長さの板を、短く切ります。
ただ切るだけと思われるかもしれませんが、実はここが一番のベテランの方しかできない作業なんです。
1枚1枚、木目や欠点(節やくされ・割れ)を確認し、欠点の部分はできるだけ捨て、使う部分はできるだけきれいな材が取れるように瞬時の判断をしながら作業しているのです。
切った材に節が多ければ、後で補修の手間がかかりますので、節が少ないに越したことはありません。そういった意味でも重要な工程なのです。
幅切り
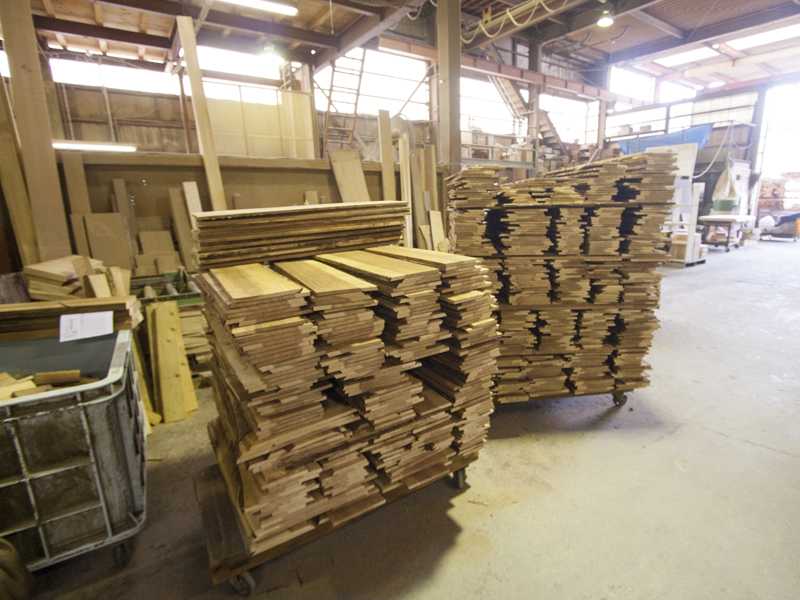
長さを切った材料(長さ約55cmの杉板)がパレットに乗っています。この材が次の幅切りの工程に入ります。
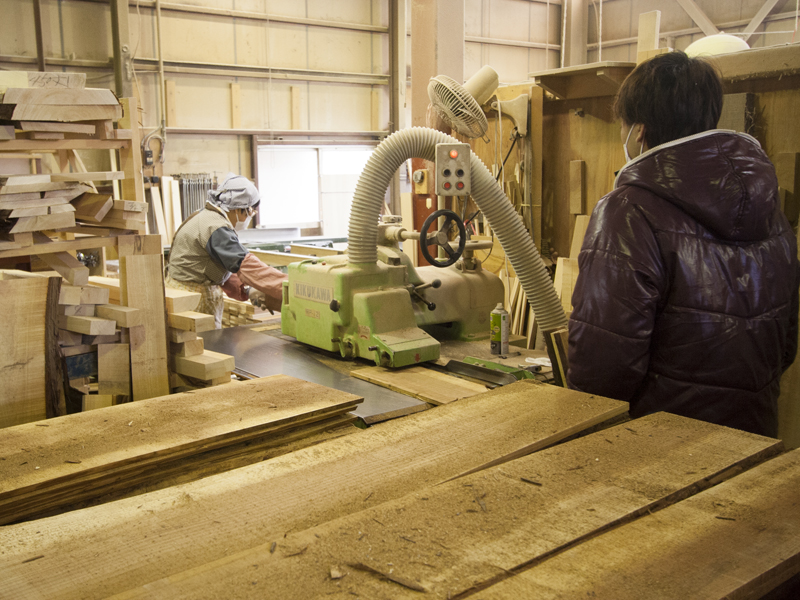
材料は右の男性が加工機械に入れて、左の女性が受け取ります。1回機械を通すと片側を切り落としますので、1回通した材料を手渡しして裏返し、2回目は反対側を切り落として、加工が完了します。
この後、材料は1)幅はぎ接着して板になるものと、2)手押しカンナ盤でカンナがけして棒状のパーツになるものに分かれます。
幅はぎ接着工程
机の天板などの幅広の材料は、実は1枚の板ではなく、幅9~10cmほどの板を並べて、接着したものです。
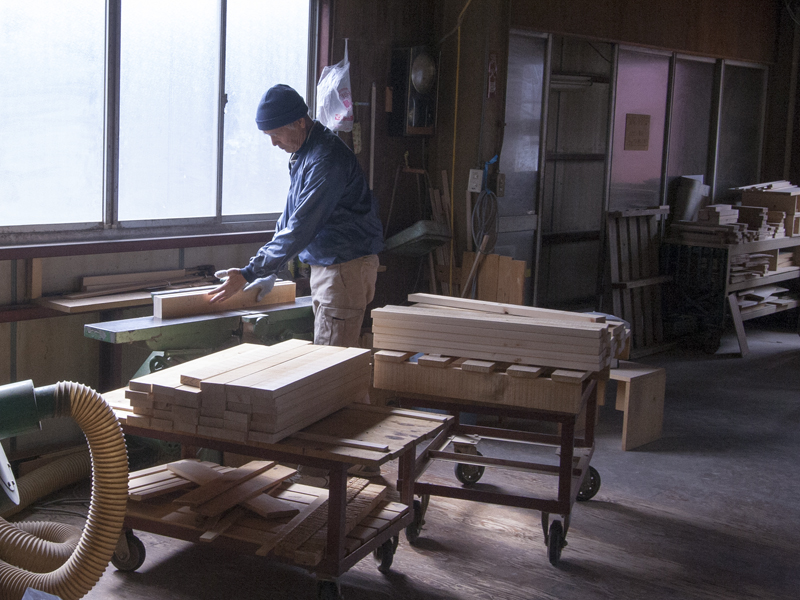
しっかりと接着するために大事なのは、板と板の間に隙間がないことだそうです。そのため、木取り工程で幅を切った材料を、さらにもう一度、手押しカンナ盤で、一直線の平面にします。この方は大工さんなので、こういった仕事は完璧なのだそうです。
ただ、せっかくここで完璧な加工をしても、時間が経つと木が動いてしまうため、できるだけ1時間以内に接着しているそうです。
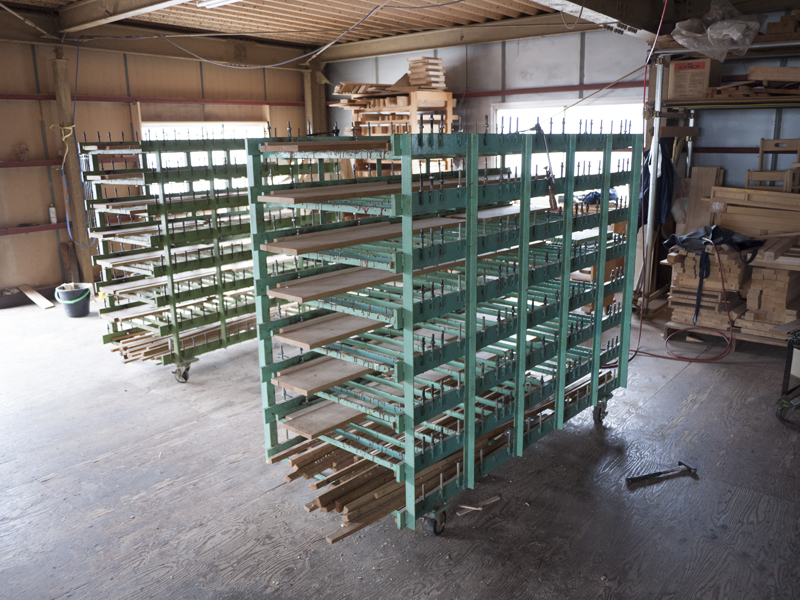
この時はちょうど作業をしていなかったのですが、この治具で幅はぎ接着をします。側面に接着剤(木工用ボンドに似た白い接着剤)を塗布して並べた後、ボルトで圧締します。1日経ったら、治具から外します。
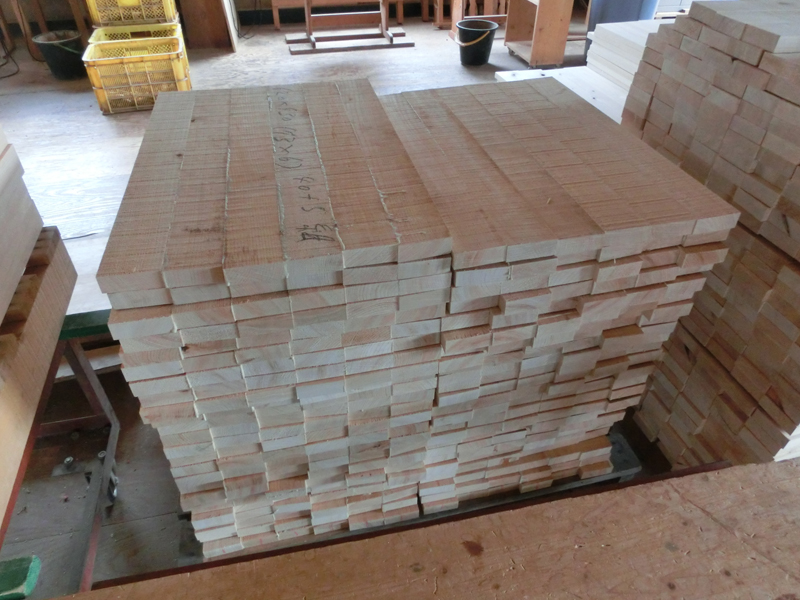
接着剤が固まるとこんな感じになります。表面は、まだ何もされていないザラザラの状態です。
厚み加工
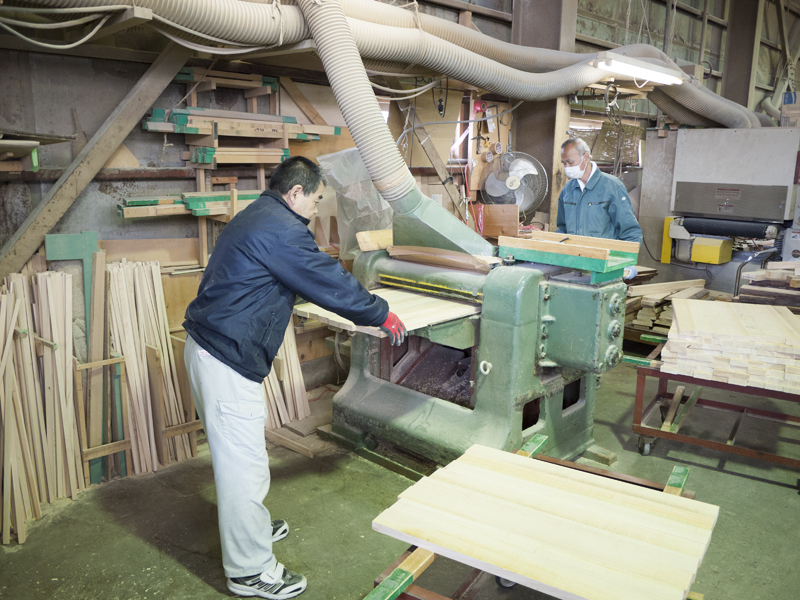
接着した後で、プレーナー(自動一面カンナ盤)で厚みを両面を削ります。写真の機械の下の部分で、カンナの刃が回転していて、向こう側から材料を入れると自動的に手前に送りながらカンナで削ります。
節を埋める
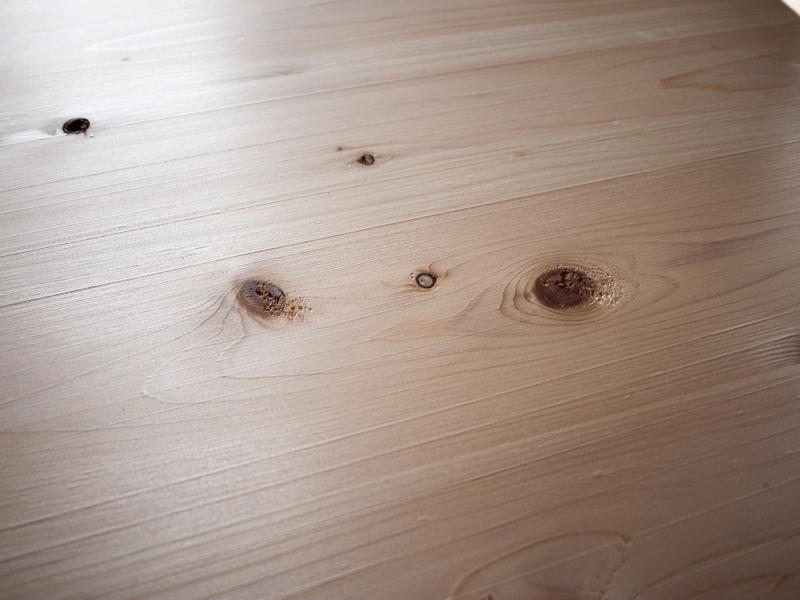
さて、表面がきれいになりました。すると節の状態がはっきりします。節は、もともと枝が出ていた部分の付け根に相当し、生節(いきぶし)と死節(しにぶし)に分けられます。
生節は、節の中身が詰まっているもの(写真中央付近)で、死節は節の中身が抜けて空洞になったもの(写真左上の黒い節)です。
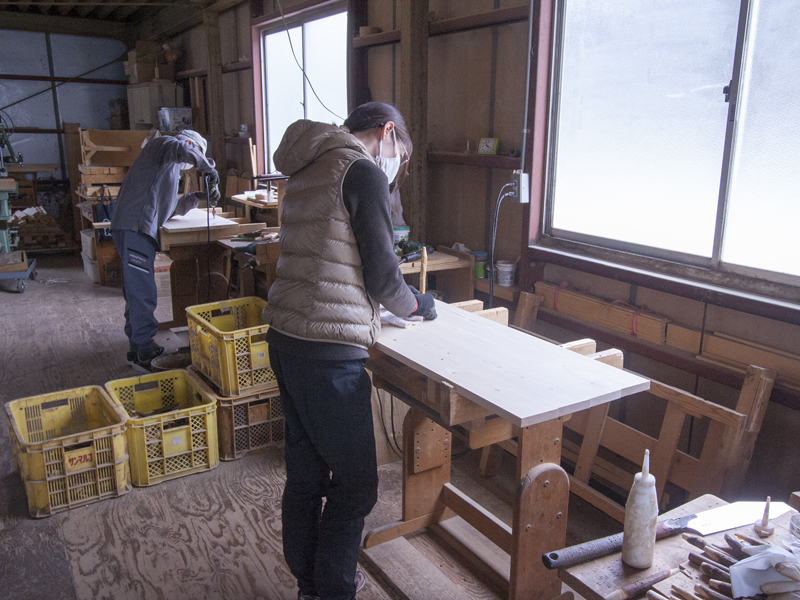
生節は堅く、抜けることはありませんが、死節はすでに穴が空いていますので、埋め木をして塞ぎます。ドリルで穴を開けた後、接着剤を注入して、ヒノキの枝をハンマーで入れ、余分な部分をのこぎりで切ります。
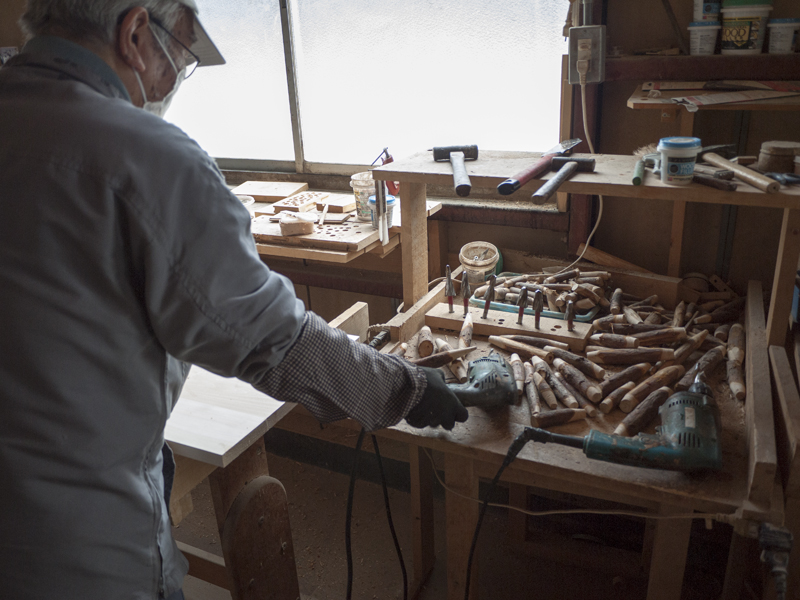
穴の大きさもいろいろあるので、ヒノキの枝もいろんな太さがあります。この枝も資源の有効利用と言えますね。
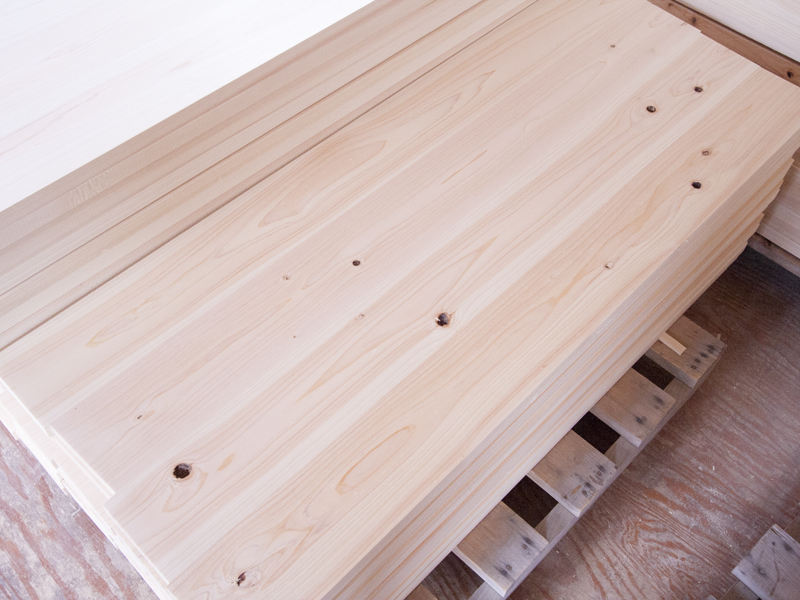
このような板が
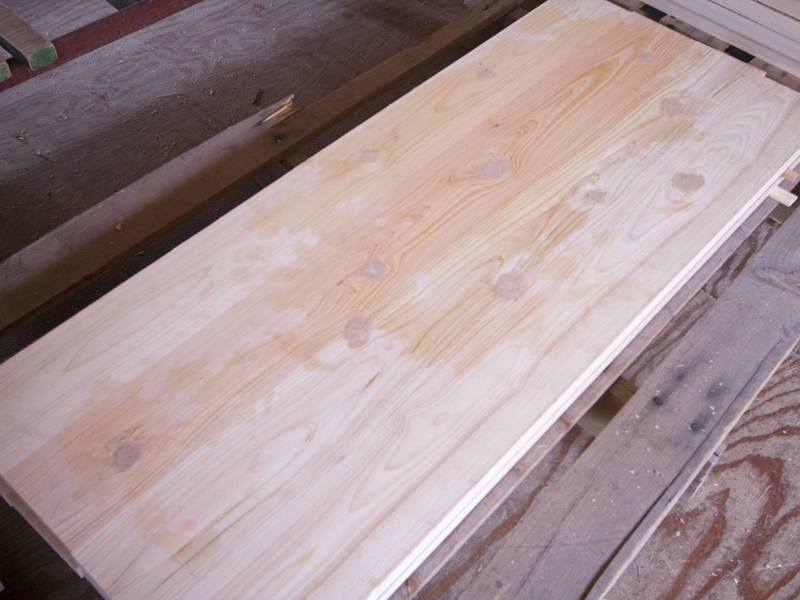
こんな感じに補修されます。節の色が薄く見えるのは、パテを塗っているため。補修した後の死節はもちろん、補修しなかった生節の部分もパテで埋めます。細かい隙間があっても、パテで埋めれば表面の平滑性が保てます。
この後、ワイドベルトサンダー(幅広の紙やすりのようなもの)で表面を平滑に仕上げます。
長物加工
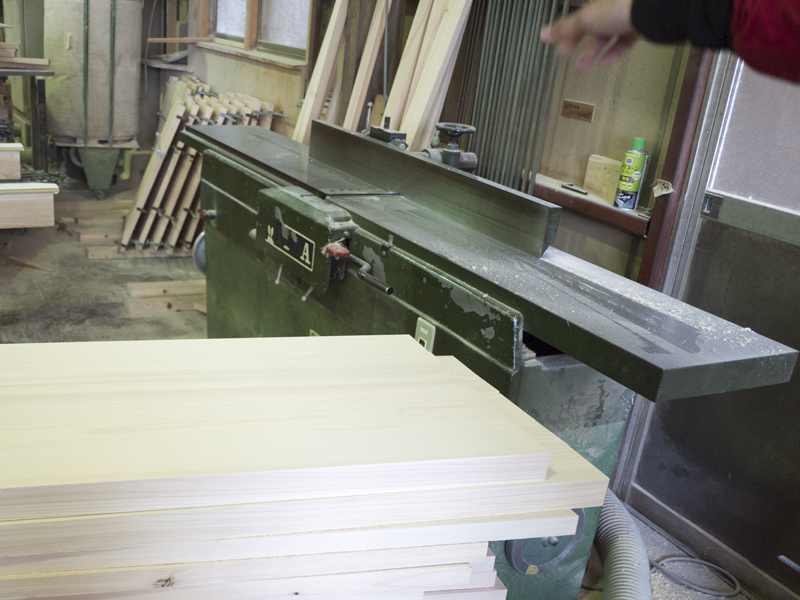
こちらは、長物用の手押しカンナ盤。断面の寸法を仕上げた後、横切りという機械で長さを仕上がり寸法にカットします。
加工工程
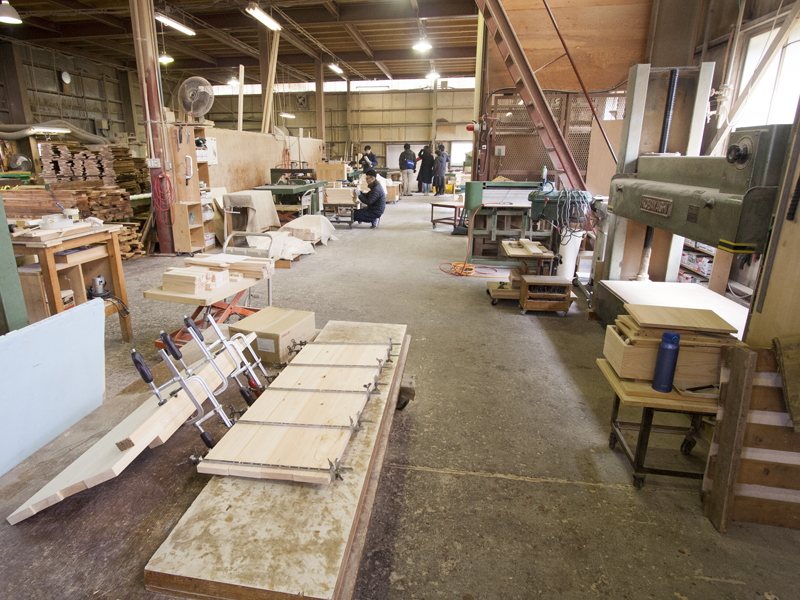
こちらでは、ほぼ正寸の厚みに仕上がった材料を、長さ決めしたり、穴あけしたり、組み立てたりします。ここでの加工精度は、そのまま商品の精度になるため、大変気を使う工程です。
面取り
板も棒状の部材も、カットしたままだと、角が直角なので、ぶつかると痛かったりしますし、木の方も痛みます。そこで、角を少し削ることを「面を取る」「面取り」と呼んでいます。
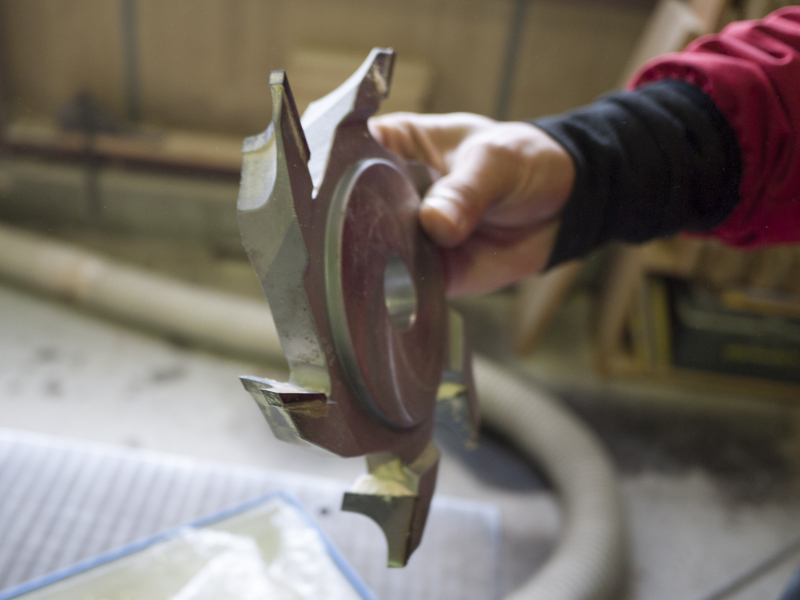
曲面にカットできる専用の刃物を使います。
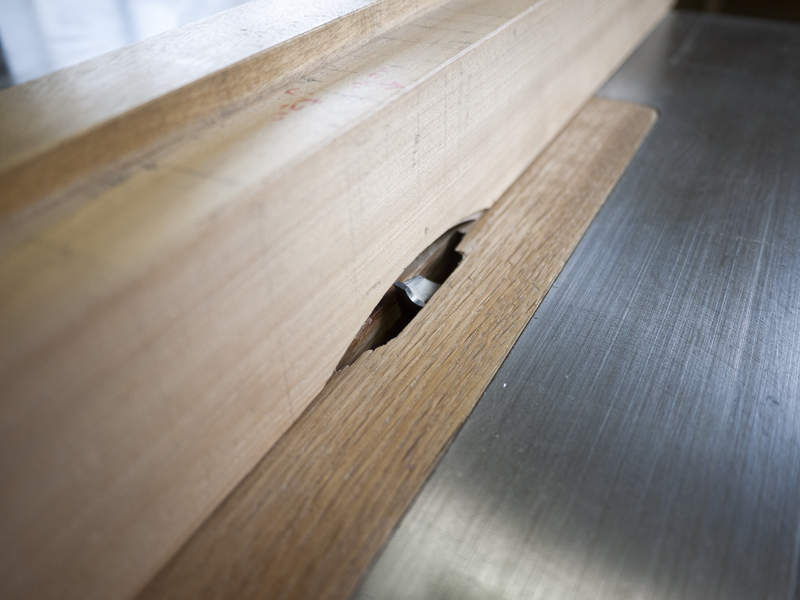
昇降盤にセットするとこんな感じ。すきまから少しだけ刃が見えています。手前から向こうに材料を送ると、刃の当たる部分が丸く面取りされるのです。
穴あけ
枠などの組み立てには、ダボを使って強度を保ちます。接着剤だけだと壊れやすいですからね。
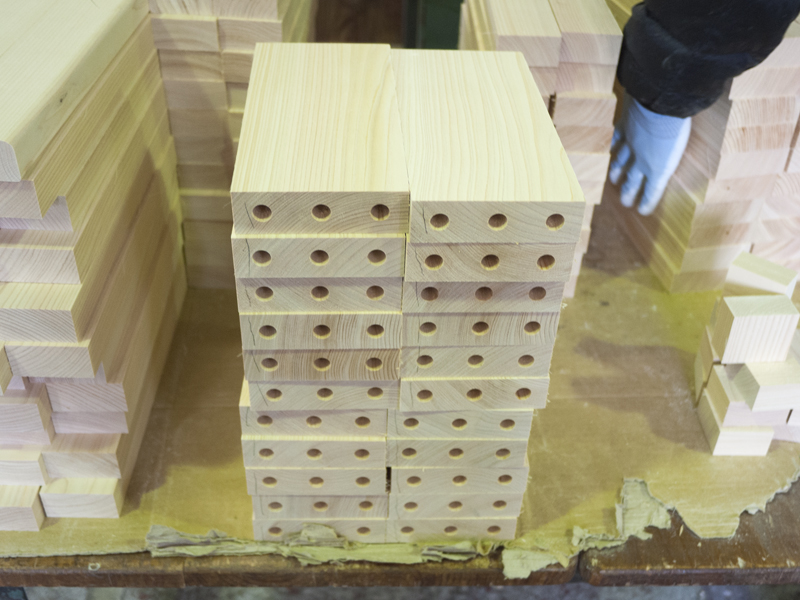
このように下穴を開け、木のダボを打ち込みます。この加工が最も精度が要求される部分で、定番商品の加工の場合は、工場長自らが作業するそうです。

今日は工場長は私たちの付き添いのため、別の方が作業されています。
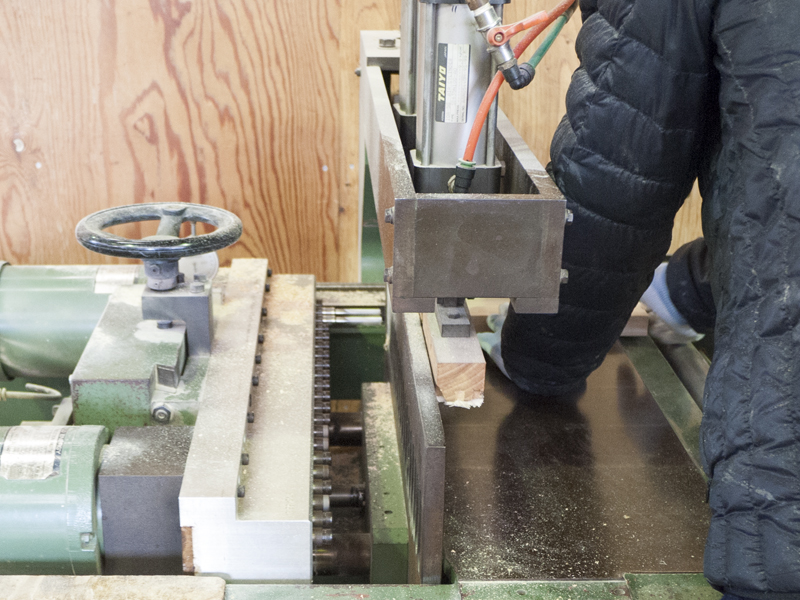
見にくいですが、画面奥に材料を押し付け、上からも押さえつけたところに、左からドリルが2本同時に移動してきます。
組み立て
枠の組み立て作業です。
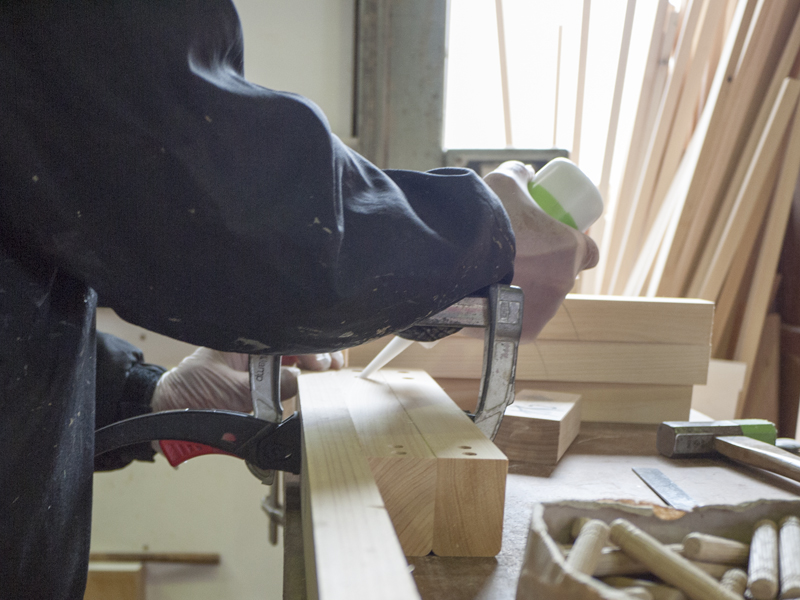
さっき開けた下穴に接着剤を入れ、ダボを打ち込みます。
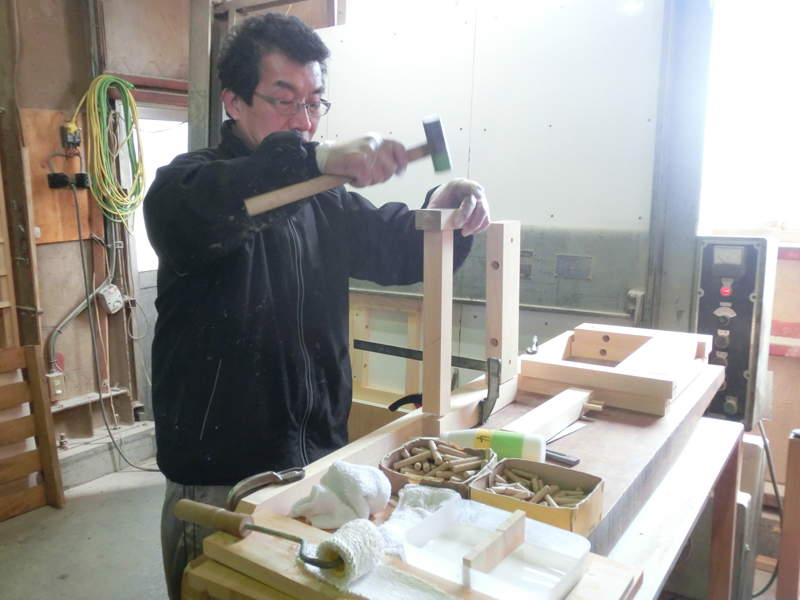
その上から縦の部材をトントントンと入れていきます。でも、最後まで入れ切ってしまわずに…
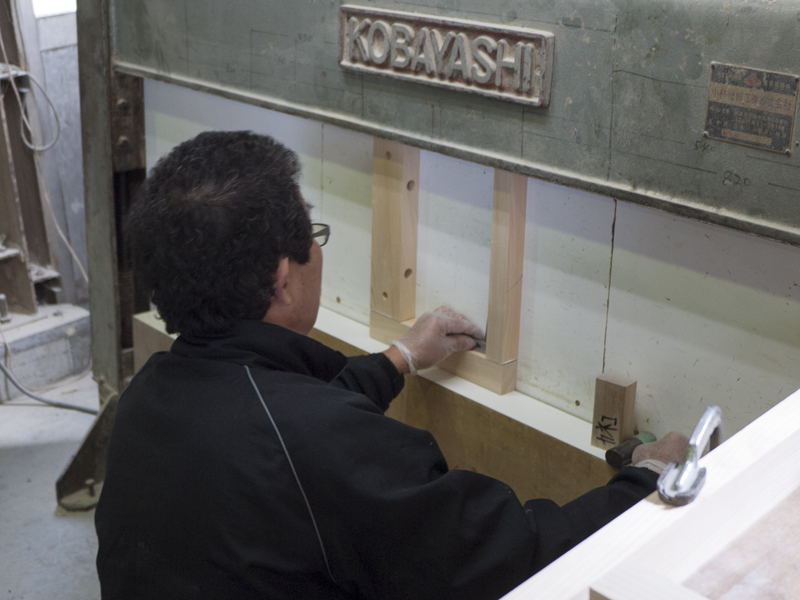
プレス機にセットして、部材同士の直角を確認したり、平らな面の凸凹がないかを確認してから、上からプレスします。
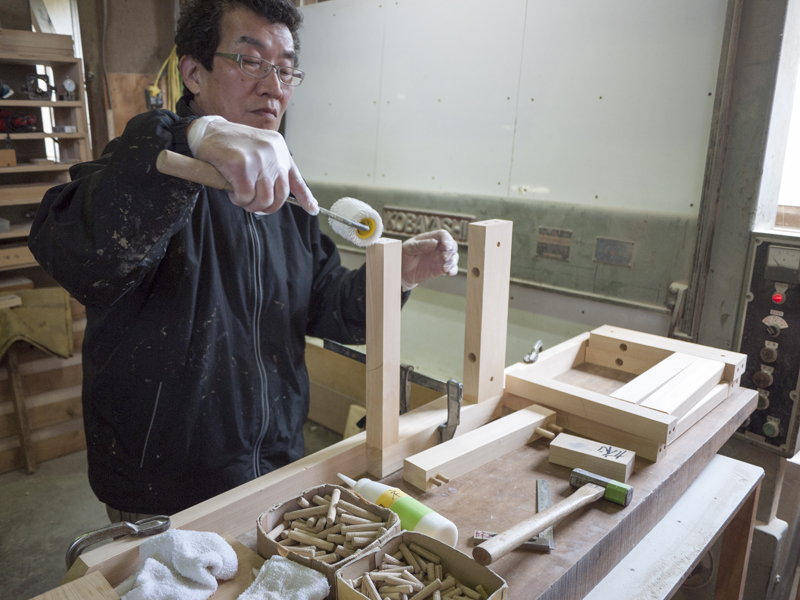
その後で、四角い枠の4本目の部材を入れます。このように棒の木口面(年輪が見える断面)に接着剤を塗っても吸い込んでしまい、接着力が弱くなるのですが、この工場では事前に一度接着剤を吸い込ませて乾かしておくことで、本番の接着時には強度が出せるそうです。
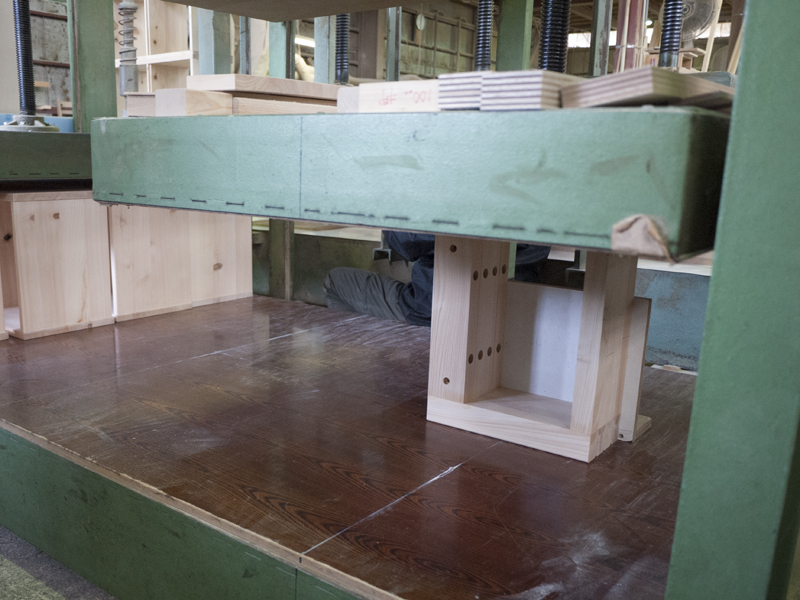
完成した枠は何本かまとめてプレス機にかけます。
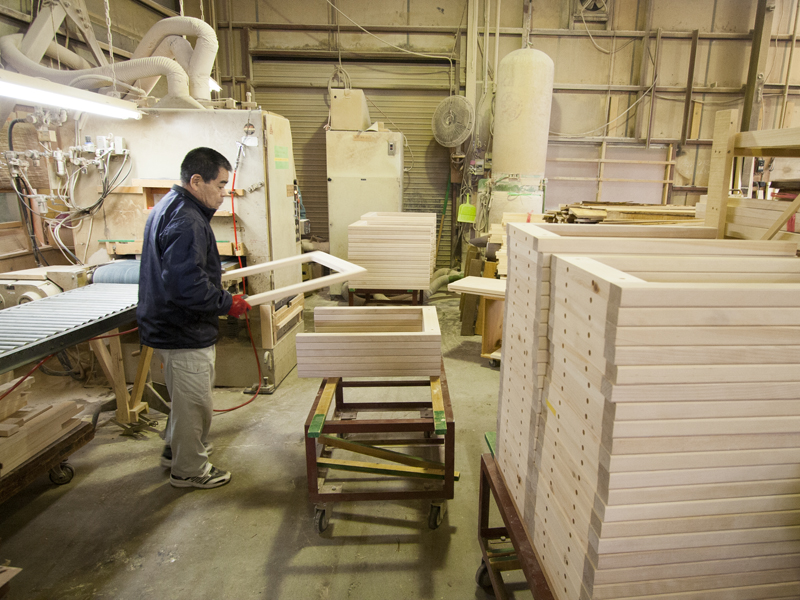
接着剤が乾燥したら、ワイドベルトサンダーにかけて仕上げます。
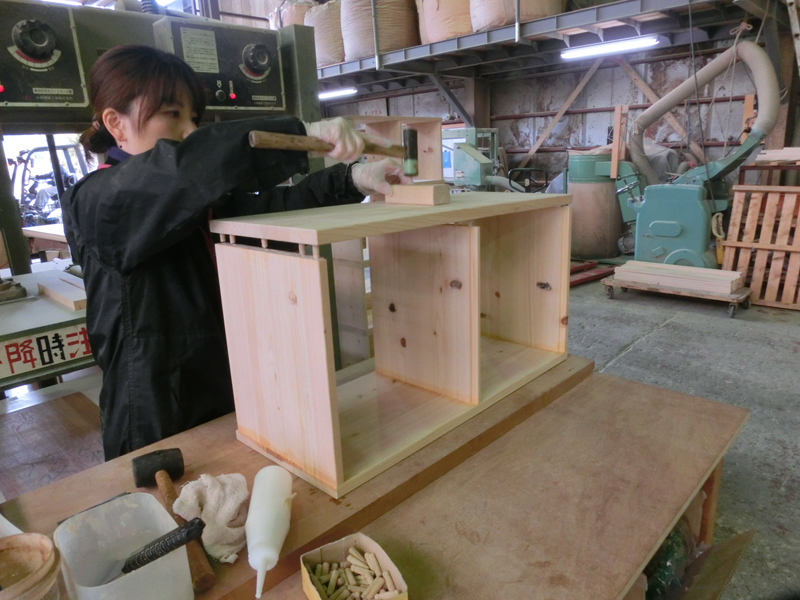
こちらは、棚の組み立て。接着剤とダボを入れて…
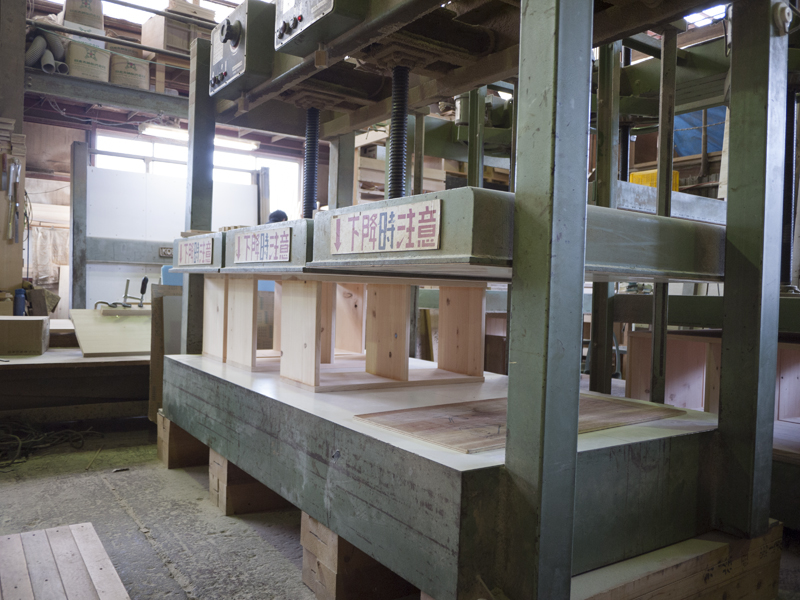
油圧プレス機にかけます。
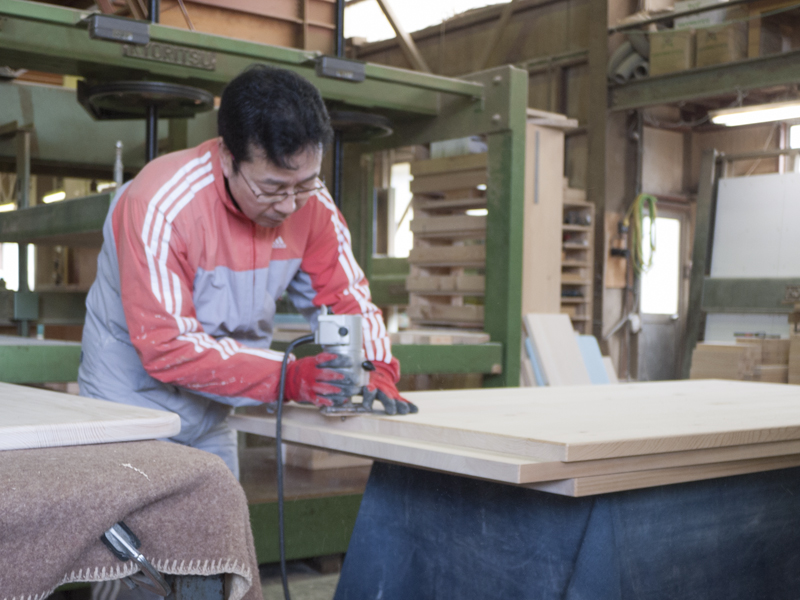
こちらは、天板の加工。パネルソーで寸法を仕上げた後、トリマーで周囲を面取りします。
この後、オイルで仕上げ、乾燥させた後、
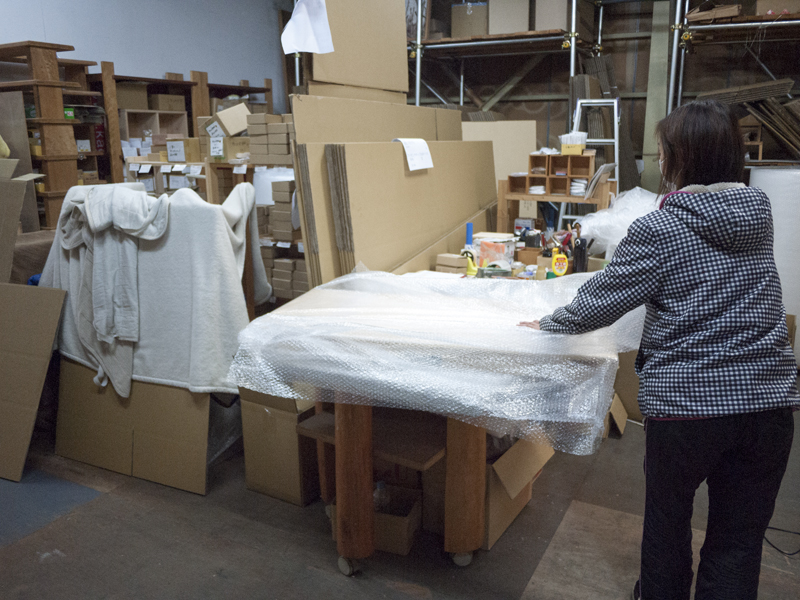
丁寧に梱包され、倉庫に保管されます。
廃材の利用
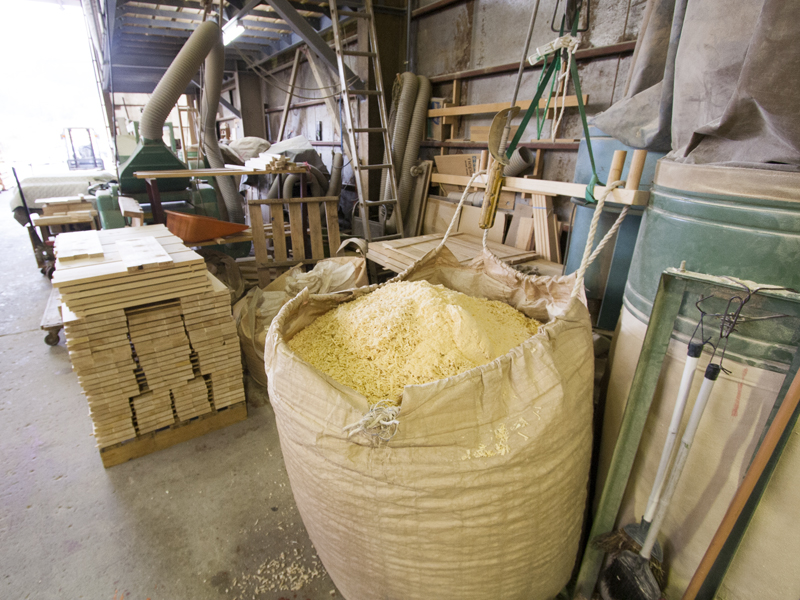
こういったオガ粉は、牧場に引き取られ牛たちの床に入れられるそうです。
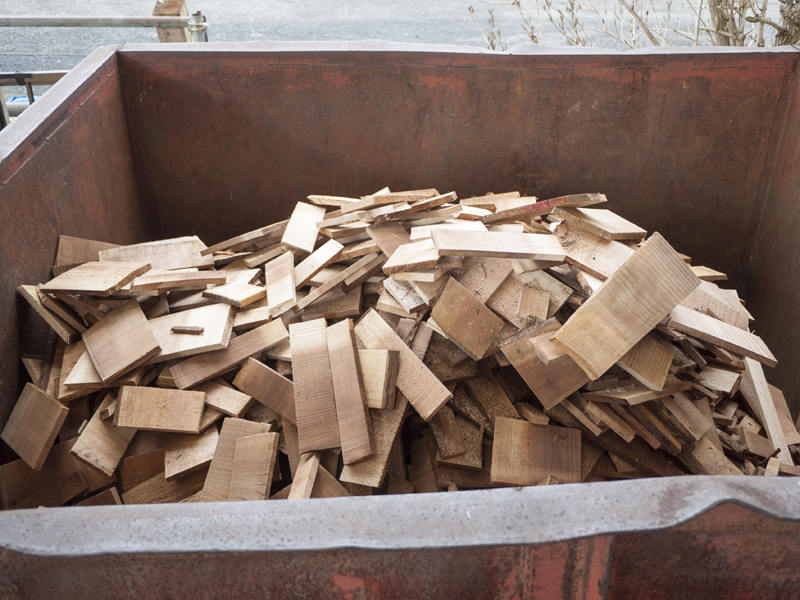
木の切れ端は、ノベルティグッズなどに利用され、それでも使えない材料だけは、工場前に置かれ、欲しい人に持って行ってもらうそうです。
工場見学を終えて
埋め木バンザイ!
埋め木の工程では2人作業していましたが、こういったところに手間をかけることで、資源の有効利用と、お客様にも納得していただける品質を両立しているところが素晴らしいと思いました。
「節がなければいい」というスタンスでは、節のあるほとんどの材が無駄になってしまいます。かと言って、「節はあるものだから受け入れろ」では、見た目や実用上の問題(凸凹がある等)が生じます。
そこに、ヒノキの枝を使った埋め木をして、その上でパテ埋めすることで、見た目も美しく、表面もつるつるの板が生まれます。この板そのものに「ものを大切にする」「資源を大切にする」という姿勢が体現されているように思います。
品質へのこだわり
「木材は生きている」と言います。空気中の水分を吸ったり吐いたりしながら、寸法が微妙に変化するのです。それは工場で加工している最中の木材も同じことです。
工場長が、「この工程は1時間以内でやります」とか「この加工は一気にやってしまいたい」とか話していたのは、まさにそれを意識してのこと。どれだけ正確に加工しても、次の工程まで長い時間放置されていたら、せっかくの精度が台無しになってしまいます。だからこそ、次の工程へ、次の工程へと素早く進むのが理想なのです。
つまり、各工程できちんと精度を出すのは当たり前で、その上で工程全体の精度を上げることを常に考えているようでした。
それはつまり、最終的にお客様にきちんとしたものを届けたい、お客様に喜んでもらいたいという思いに発するもので、私も「こんなに一所懸命作ってくれているんだ」とうれしくなりました。そして、安心してお客様に販売できる、と確信しました。
最後になりましたが、時間をかけて丁寧に説明してくださった工場長、大勢で押し掛けたにも関わらず、にこやかに迎えてくださった工場の皆さん、どうもありがとうございました!
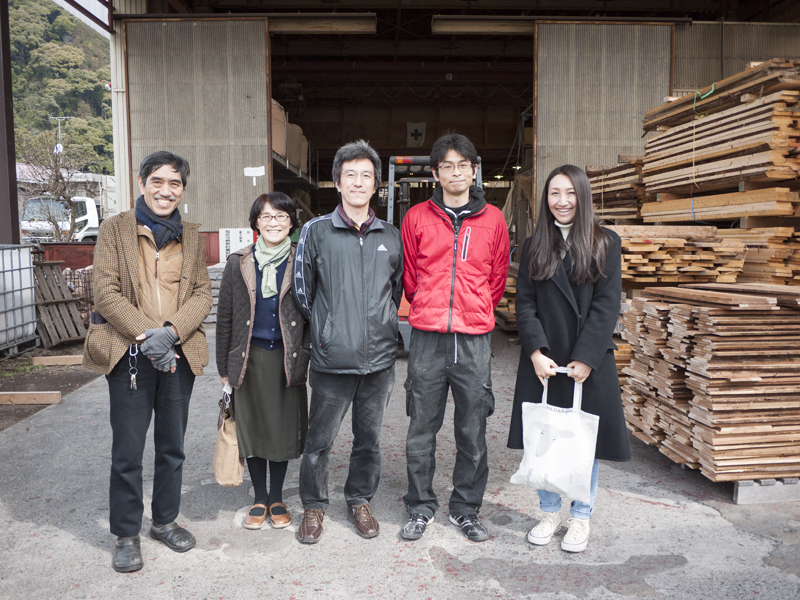
山梨工場長(赤いジャンパー)と一緒に記念撮影。